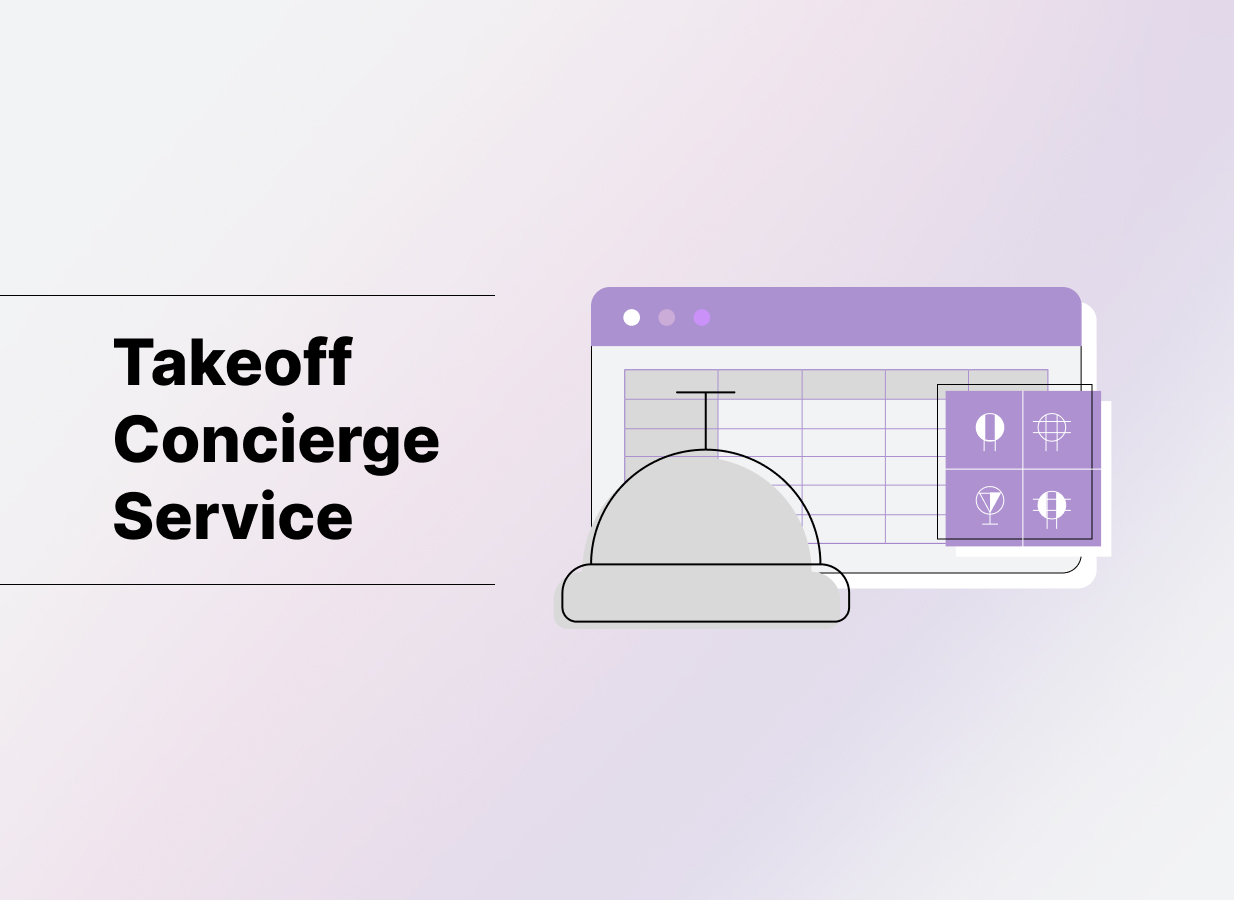
Electrical Estimating Basics - From Documentation to Cost Evaluation
Welcome to the electrical estimating training blog! This series of posts is intended to serve as a resource for junior electrical estimators and those considering the role as a career.
Estimating and the Role of the Estimator
The role of an estimator is to determine the cost of a project. If the estimate is too high, the company will lose the project to a competitor. If it is too low, the company will lose money if it wins. The estimator's job is to determine a cost projection as accurately as possible within the given time frame. The time constraint is key, as bids often need to be produced within one to two weeks, which doesn't allow for highly detailed planning and analysis, especially when using traditional processes. A key part of an estimator's job is to find fast methods to produce an accurate cost, often using averages or rules of thumb that produce results that are close enough.
Estimating occurs in two major phases. The first phase is takeoff, where you review the plans and count or measure the entire electrical scope. The second phase is referred to as estimating, even though both takeoff and estimating are part of the overall estimating process. In the second phase, the outputs from takeoff, including counts and measures, are converted into detailed labor, equipment, and material requirements, which are then priced to determine the cost.
For many trades, takeoff primarily involves counting and measuring the materials and components that are designed. That's partially true for electrical estimating, as power devices, lighting fixtures, and some lighting controls are often depicted on drawings; however, the routing between the equipment, panels, and devices is frequently not designed. The electrical estimator must design the routing and must often calculate the wire sizes. An electrical estimator does much more than simply counting, measuring, and pricing.
Estimating at Different Design Stages
Estimates must be produced at various stages of the design process. The inputs received and the scope of work depend on the design phase. In early-phase work, specifically the schematic design stage, the only input may be the architectural background, with no electrical components at all. The estimator must either use averages, such as the typical cost per square foot, or lay out the devices and then perform a more detailed takeoff.
During the middle phase of design, referred to as the design development phase, the devices are shown, but typically not assigned to a panel or circuit. Again, the estimator either uses averages or must make assumptions and design the rest of the system. In the final phase, construction documentation should include all devices and equipment, which should be assigned to a specific panel and circuit. Even in this phase, the estimator generally must design much of the routing.
Work may continue after the 'final' design as changes or additional information will continue to be released in addenda, which must be analyzed by either the estimator or the project team.
The remainder of this post will focus on the latter stages of design. Early phase processes will be a topic for future blog posts.
Inputs to the Estimating Process
A lot of information is required to complete an estimate. When assigned to a project, the estimator typically receives the:
- Request for Proposal (RFP): indicating the scope of work
- Construction drawings: defines the what and where
- Specifications: defines the allowable materials, methods, etc. Specifications constrain the what and the how.
- Project schedule: describes the when, which can have a dramatic impact on cost, as we'll explore in future posts
- Equipment lists/cut sheets: provides detailed information about equipment to be installed
- Optionally, management may provide specific instructions on how to approach the project and the methods of construction that should be used
RFP/Narrative
An RFP gives a basic overview of the scope of work the estimator must price. For the electrician, this would typically include information about the building's size (in square feet), its usage type (food service, medical, institutional, etc.), and possibly some basics of the service (including the secondary voltage to be utilized off the utility transformer and the total amperage size of the service). A narrative would provide further explanation of aspects to consider for pricing, often in lieu of usable floor plans.
Construction Drawings
Construction drawings, also known as plans or blueprints, are large-format plans that graphically depict the location of electrical equipment and devices on top of an architectural background, accompanied by supplemental diagrams and schedules.
Specifications
A document, often hundreds of pages or more, that defines constraints and requirements governing how the scope defined by the RFP and construction documents may be achieved. The specification defines the type of materials (and many times the allowable manufacturers of those materials) to be used on the project, as well as more specific installation requirements or other constraints.
Preliminary Project Schedule
The project schedule is often represented as a Gantt chart or a spreadsheet. It contains major milestones for trade handover points, at a minimum, and may include additional details. The timeline of the project is important to understand how much manpower you need to consider for the lifetime of the project and for jobsite provisions like storage trailers, on-site office facilities, heavy equipment rentals, and other things dependent on durations.
Equipment List/Cut Sheets
Sometimes, a list of equipment to be installed is made available, along with pertinent electrical information required to determine wire and conduit sizing. Cut sheets provide details regarding specific pieces of equipment that might determine other installation needs or auxiliary components required. One example is a manufacturer's cut sheet for an MRI room, which would include load information for the equipment, its specific power distribution needs, communications components, and installation requirements that prevent damage to the electrical system due to the intense magnetic field it creates.
Other Information (geotechnical reports, site logistics, sample contracts, approved vendor list, etc.)
Numerous other documents may be provided that might influence the cost. The existing site conditions may require special equipment, sample contracts might include legal requirements or qualifications that come with additional fees, and an approved vendor list that may limit your options for collecting pricing.
Next Up
In the next post, we'll cover the definition of an electrical system, the major components of typical systems, and how the components and subsystems work together to power the building.